16个月造出海上风电顶流“巨星”
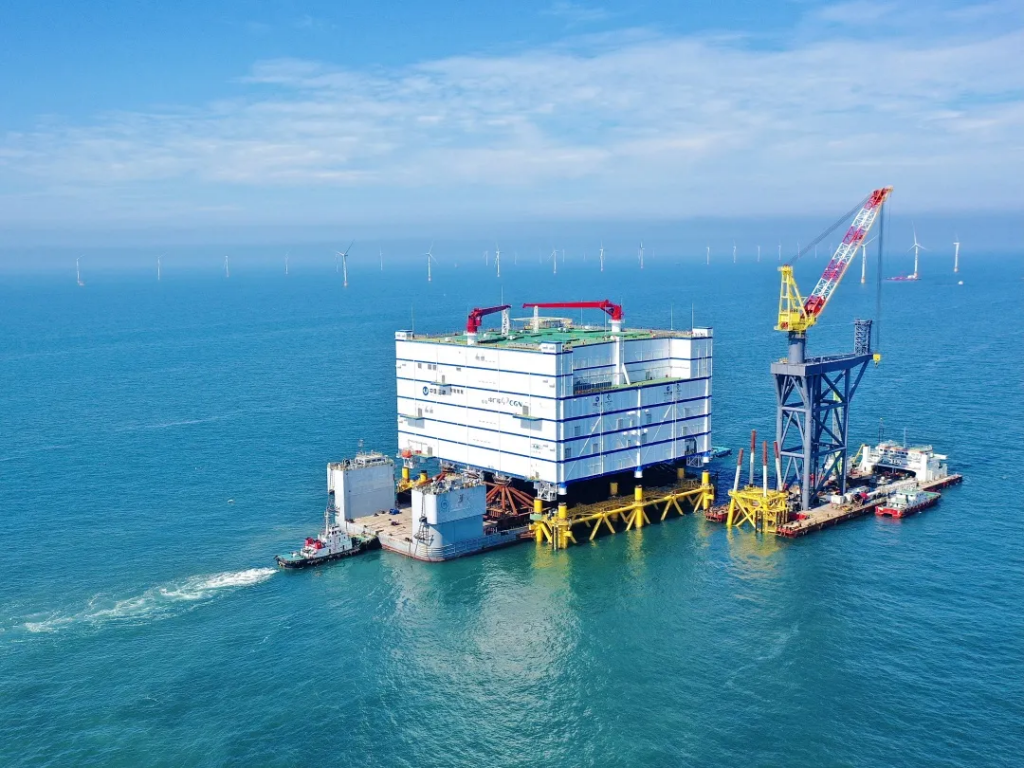
如东海上换流站工程包含基础桩、导管架及上部模块三大部分,振华重工负责全部的建造、运输和海上安装任务。其中,换流站上部模块长89米、宽84米、高约44米、重2.2万吨,每层的面积近乎标准足球场,高度约15层居民楼,重量接近7至8个升压站总和。
海上换流站共有7层,类似建筑性工程,如果采用盖楼房式施工方案,即一层一层地搭载,不仅工期无法保障,且施工安全压力极大。在项目前期碰头会上,项目团队创新性提出“模块搭载、分层搭建”的施工方案,即首层搭载完毕之后,将二、三层进行合拢,然后再集中拼装。振华重工海上换流站项目执行经理李树清介绍,“这套方案的灵感来源于乐高积木,二、三层是一个完整的阀厅,中间牵涉到的模块交叉施工较多,采用‘小合拢再搭建’的方式,既可以减少重复焊接,提高模块搭载的对位精度,还可以实现双线施工、低空作业,提高了施工效率。”
施工思路敲定后,项目团队进行了细致周密的部署。2020年2月,项目正式开工,于3月15日开始首层模块车间制作;4月26日实现首层15个分段全部上胎。与此同时,项目二、三层的生产工作也步入正轨。7月底,项目开始进行上部结构外场搭载,比原计划提前了4天。
外场搭载施工完成,项目转入模块内部施工。海上换流站1到3层为阀厅,三个深海风电场共1100兆瓦的电能将通过阀厅深层处理,转换成损耗更低的直流电。负责“深层处理”工作的高精密设备——换流阀必须长期处于恒温恒湿环境中。“比起外场搭载,阀厅内部精装的难度更大,对安全施工管理要求也更高。”项目安全主管徐晶晶说。
为了满足恒温恒湿的条件,项目团队要在高20多米的阀厅四壁安装消音、隔热专用膜,传统方法通常采用“由下往上”依次搭建施工脚手架的方式进行施工。“按照传统方法,阀厅里大量高精密设备必须等到墙面精装完毕、脚手架拆除之后才能进场,不仅耽误工期,且成本花费很高。”徐晶晶说。为了提高施工效率,项目团队进行“头脑风暴”,提出了“模块化”脚手架搭建方案,即高空作业时采用悬挑脚手和倒挂脚手搭设方式,提前在无平台区域和设备舱顶区域搭设好悬挑脚手架,实现脚手搭设分段模块化。悬挑脚手工装与本体之间设计为螺栓柔性连接,避免后期拆除油漆破损,实现了阀厅各模块搭载与高精密设备进场安置的同步化,极大地提高了施工效率。
阀厅封顶完成,项目团队迎来了最难、最危险的节点——顶盖倒挂脚手架拆卸施工。“我们要在22米的高空完成顶盖倒挂脚手架的拆除,难度极大,安全风险极高。”徐晶晶说。项目团队从100多名脚手架施工工人中选出10位工作经验10年以上的“专家级”工人,负责本次顶盖脚手架拆卸任务。除了为工人配备五点式安全带,项目还设置了安全兜网,进行安全二次兜底。
2021年1月,顶盖倒挂脚手架首次拆除施工拉开序幕。李树清、徐晶晶等人一大早就赶到施工现场,在施工区域来回巡视,监督工人们佩戴好安全装备。开始施工后,只见工人们在安全绳的牵引下,像“蜘蛛侠”般行走在脚手架平台上。他们先从方形顶盖的四个边角拆除脚手架,再拆除中间部分。拆到最后,工人们只能站在仅有的两根铁管上操作。看着他们高空作业,大家的手心里都沁满了汗。当最后一根脚手架拆卸归位,工人们返回到安全区域时,徐晶晶悬着的心终于放下了。
“拖、拉、拽、移必须统统上场,才能请动它。”在前期的换流站装船工艺研讨会上,有人如此打趣道。原来,海上换流站在南通振华重装码头后场完成总装后,它距离码头前沿约214米,上船后还需再继续滑移106米。如何让总重量近2.8万吨的“庞然大物”跨越300多米距离,成功登船,考验着振华人的智慧。
为了让这个“庞然大物”挪动身子,振华重工海服研究院海工运输安装设计部经理李辉使足了“巧劲儿”。李辉为换流站定制了长度100米的5条滑轨,并排摆放,借用液压锚机的牵引,让换流站通过5条滑轨自己“走”到码头前沿指定位置。“为了将换流站的重量平均分散到每一条滑轨上,我们对码头承载、牵引能力、滑移过程纠偏等数据进行了精确计算,全程监控滑移装船过程中轨道应力变化。”李辉说。在项目团队努力下,经过17天的日夜奋战,如东海上换流站终于迈着“蹒跚的步伐”,顺利滑移上船。
如今,通过采用振华重工国内首创的重型设备双片独立导管架高位浮托安装法,这座顶流“巨星”顺利完成上部模块与下部导管架的毫米级对接,“扎根”深海,为136万户家庭年用电及国家“3060”双碳目标效力。
责任编辑:牛淋淋